Robotics has a long history, but with the co-occurrence of technological advancement and global aging populations, it is now an effective technology for improving productivity across many sectors, especially during economic uncertainty. The power sector is no exception in turning to robotics to increase the productivity and safety of its workforce.
According to GlobalData’s Thematic Index, robotics will continue to impact the power sector as robots are increasingly deployed for safe inspection, maintenance, and more disruptive use cases, such as installing renewable energy infrastructure. However, robotics in the power sector is still in its early stages.
Only with a digitalisation plan that embraces multiple emerging technologies (e.g., edge computing, IoT, cybersecurity, and AI) can power companies form the interconnected ecosystem needed to access the full operational benefits of robotics.
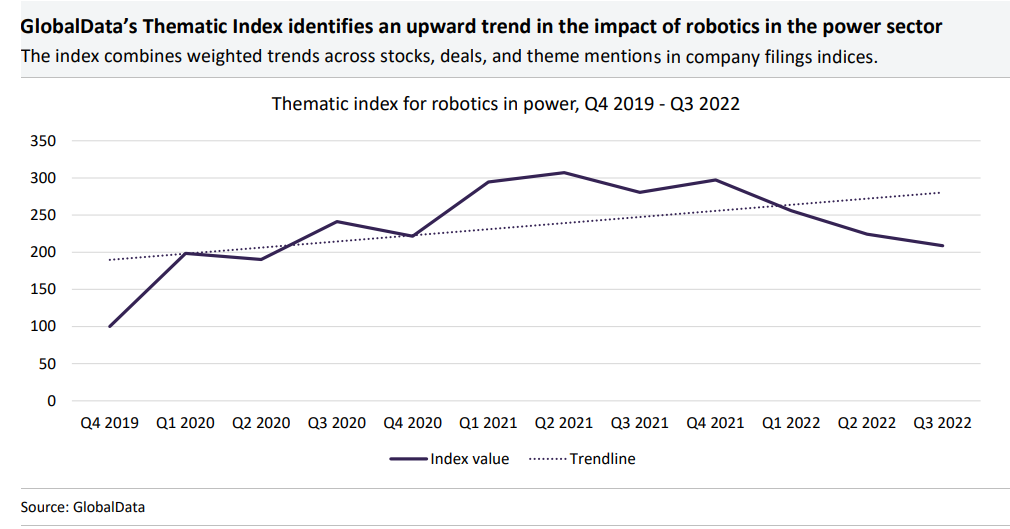
Within the array of emerging technologies, robotics has much to offer. The matrix below details the specific segments of the robotics value chain where power companies should focus their time and resources. We suggest that they invest with high priority in technologies shaded green, with medium priority in those shaded yellow, with low priority in those shaded red, and ignore areas shaded grey.
For example, the rationale behind power companies investing in semiconductors as a low priority at all stages of the value chain is that it is a hardware component with a limited number of known specialist producers (including Qualcomm, Apple, Intel, and Nvidia). It would be unnecessarily complex and costly for power companies to develop semiconductors in-house.
Power companies should only invest time in choosing the chip suppliers with the lowest risk of supply chain disruptions. Conversely, the other hardware segment of the robotics value chain – precision mechanical parts – has many specialist vendors and constantly emerging start-ups.
Therefore, power companies should invest more time and resources here (medium priority) to ensure the correct parts are selected, preferably for the most interoperability throughout their operations.
The software section of the robotics value chain is encompassed in the term robotic intelligence. This has become increasingly important in recent years, with robotics companies moving away from having proprietary and closed software to open-source robot operating systems (ROSs).
This has enabled the emergence of next-generation robots in which AI is integral. Power companies must invest in these AI-led robots that employ open-source ROSs as a high priority. This will improve interoperability between their different robotics products, enable data sharing for robots with better algorithms and control systems, and ensure these robots are designed and trained for relevant power industry use cases.
Power companies that invest in robotic intelligence now will not be playing catch-up when robots move onto the use of neuromorphic processors that operate more like a human brain than a traditional chip and perform assigned duties using associations, acquired skills, and probability.
Jumping ahead to the robotics as a service (RaaS) segment of the robotics value chain, power companies must also invest here as a high priority to not fall behind. For power companies, this presents an ideal method to deploy robots that are constantly learning and easily scalable across their geographically dispersed sites.
Around robot manufacturing, many valuable investments can be made at different stages of the power value chain. For example, drones can visually inspect power infrastructures, and industrial co-bots assist in demolition and tunnelling works at power sites.
However, among all segments of the robot manufacturing section, inspection, cleaning, and maintenance robots have seen the most widespread and impactful use in the power sector. For example, inspection robots can spot equipment faults early and reduce the need for downtime. These robots can also deliver a level of accuracy that humans cannot always provide and improve safety as inspection sometimes requires access to dangerous locations.
Some inspection and maintenance robots can go beyond spotting faults to resolving them by manipulating objects, e.g., opening or closing valves or activating switches. Power companies must continue to invest in inspection, cleaning, and maintenance robots as a high priority to unlock their full potential in improving productivity, lowering operational downtimes, and prioritising worker safety.
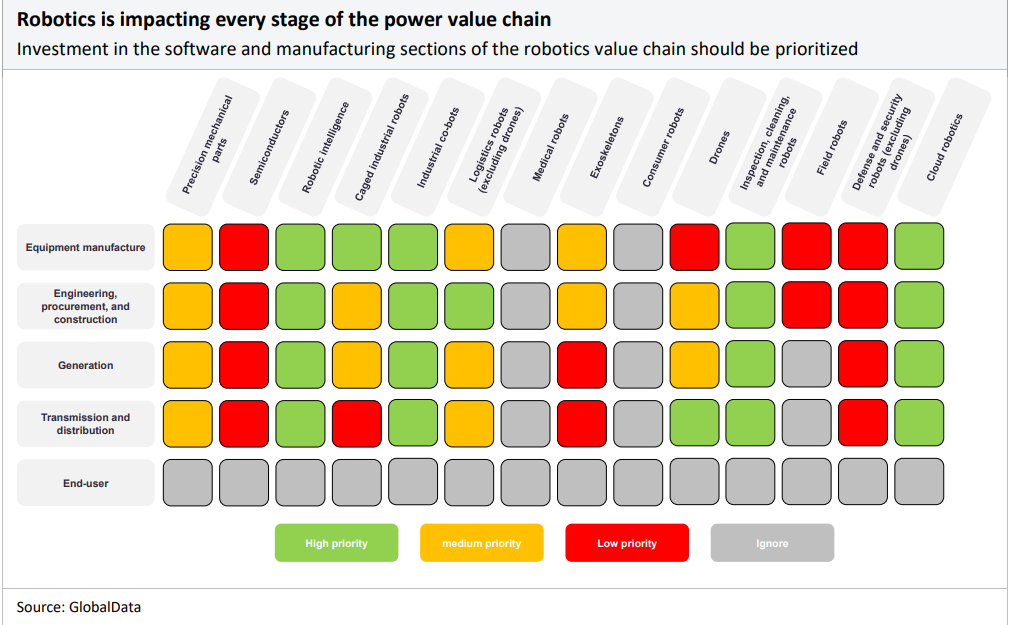
GlobalData, the leading provider of industry intelligence, provided the underlying data, research, and analysis used to produce this article.
GlobalData’s Thematic Intelligence uses proprietary data, research, and analysis to provide a forward-looking perspective on the key themes that will shape the future of the world’s largest industries and the organisations within them.