From improved asset availability to improved competitive advantage – the increasing customer value of IOT maintenance solutions in gas turbine operation & maintenance.
Over the past years many gas turbine operators have tried to improve their operational results by implementing IOT-based maintenance solutions that promise immediate improvement of day-to-day gas turbine operation & maintenance. Operators who have worked with these systems have experienced that such applications do not always bring the value they had expected from them.
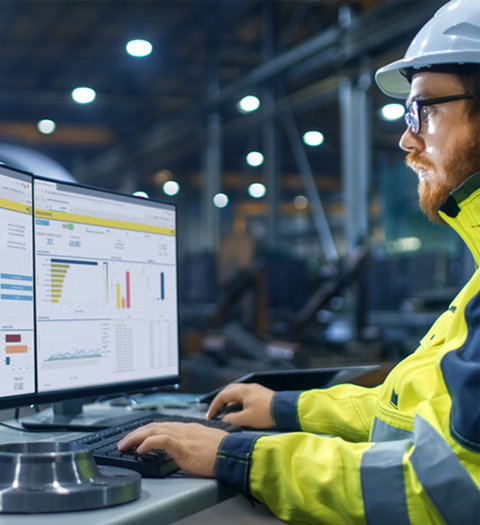
Well-implemented IOT-based maintenance solutions can provide three levels of customer value to gas turbine operators:
Improved asset availability
At this level the added customer value is more effective and more cost-effective maintenance which is reflected in increased first time fix rates, faster response and turnaround times and lower % travel time vs hands on wrench time.
Improved lifecycle cost
At this level the added customer value is lowering the total cost of ownership of a gas turbine operation by looking at the total OPEX structure of the operation, e.g. increasing engine efficiency to realize savings on fuel consumption.
Improved competitive advantage
At this level the added customer value goes beyond the OPEX structure by co-creating new value propositions and new business models based on smart utilization of the gas turbine assets and smart cooperation with market parties.
It is essential to understand that IOT is a tool. IOT will not deliver any added value itself. You need to be able to utilize an IOT tool to create added value. This means that whomever will work with an IOT system, they will need to learn how to utilize this powerful tool in an effective way to create the required added value to their business process.
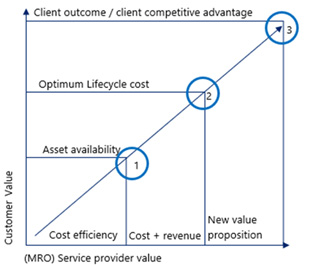
Improved asset availability
For most gas turbine operators improved asset availability (level 1) is the key driver to invest in new IOT-based maintenance solutions, most often in the form of remote monitoring and diagnostics applications. Unfortunately many of these applications focus on technical data (re)presentation and offer limited support for quick and effective day-to-day decision making in operation and maintenance. As a result the on-site acceptance and practical use of these solutions remains limited as well which creates a real challenge for those companies want to make the step from the first improved asset availability level towards the second improved lifecycle cost level.
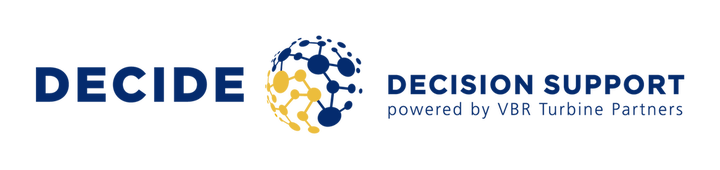
DECIDE decision support
DECIDE remote decision support for gas turbines is an IOT-based maintenance solution that works from a different perspective: human operator understanding.
For many gas turbine operators and maintenance managers the preferred way of working is:
- To have 24-7 dashboard overviews of the overall status of their operation;
- To receive timely and correct signals when something is about to happen;
- To receive easy-to-understand practical recommendations how to act on these signals in the most effective way.
DECIDE is a smart maintenance service. VBR provides dedicated software and a means to analyse the condition of the gas turbine asset. What makes the difference with most other providers of IOT solutions is that our technical specialists support our clients by transforming the initial data output of the system into a concrete maintenance strategy that is supported by 24/7 dashboard overviews and easy-to-understand practical maintenance recommendations. This enables gas turbine operators to take the right decision at the right time, every time again to realize their business goals. With DECIDE we make the in-depth technical maintenance expertise of VBR immediately and easily available for our customers.
Learn more about DECIDE?
VISIT OUR WEBSITE
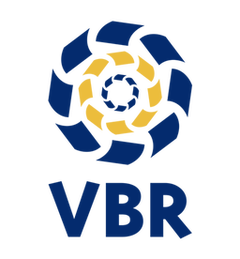
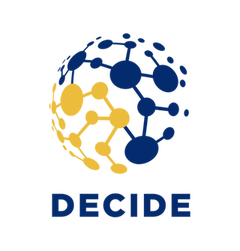
Author: Patrick Jansen, business unit manager DECIDE decison support, VBR Turbine Partners.