STAY OPERATIONAL DURING PLATING REPAIRS
/ Improve your asset availability and return on assets with wider use of selective plating /
Selective plating has long been the plating solution of choice for maintaining turbines and generators within the power generation sector. For creating a robust surface finish which meets the optimum performance requirements for critical components, selective plating is the preferred method for many industry leaders such as Siemens, GE, MHPS and others. A flexible, portable and highly efficient process when compared to tank plating, selective plating has proven a worthwhile investment for original equipment manufacturers and repair specialists alike.
Significantly reducing the volume of chemicals required, compared to tank plating and producing less waste, selective plating is a highly mobile, incredibly flexible process which allows repairs to be carried out on-site. This improves the cost and time effectiveness of making repairs to critical components. It enables facilities to remain operational and improve their return on assets and asset availability.
A fast and effective solution in time-critical applications
Selective plating allows operators to accurately focus the plating onto specific areas of a component, enabling parts to be plated on-site. This can drastically reduce downtime and minimize production and maintenance delays, which is especially beneficial for applications where turbines or generators need to be returned to service in a time-critical fashion.
In contrast to tank plating, selective plating does not require extensive masking or special fixtures to plate the component. The length of time a plating operation will take is determined by the size of the part and the thickness requirement. In market-leading selective plating systems, deposits can be plated at rates that are 30-60x faster than conventional tank plating. Selective plating also allows for plating of areas on parts that are too large to fit in a tank.
The performance and cost differences that these factors can make to maintaining, enhancing or repairing critical components can be significant.
Multiple coatings available using one process
The selective plating process is suitable for repairing a variety of critical turbine or generator components and can be used for an extensive range of applications, including improved corrosion protection, wear resistance, electrical conductivity, and enhanced lubricity, while increasing performance and in-service life. Deposits include zinc-nickel, nickel, nickel-tungsten, cobalt chromium carbide, silver, gold, platinum and more.
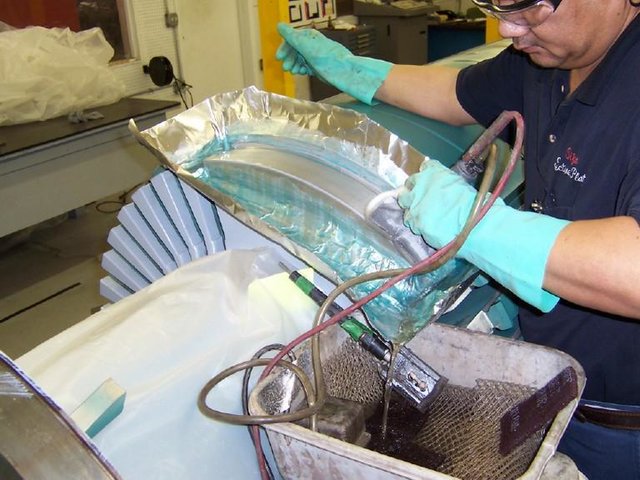
Automating the process to eliminate operator error
Did you know, while selective plating can be carried out manually, through advancements in automation technology, repair facilities and manufacturers can now achieve even greater quality and consistency by eliminating operator error and optimizing the deposit properties? With the use of programmable power packs operators can use standardized plating parameters that include volts, amps and ampere-hours for consistent deposits from component to component. This data can also be captured and stored for seamless quality control.
A proven alternative to other coating methods
In the power generation industry, technicians and engineers have multiple repair options that can be used depending on the component’s size, location, and damage. Yet each process has its disadvantages when compared with selective plating. For example, one budget-conscious customer needed to resize the bearing diameter of a 42.5 inch thrust block. Sleeving and flame spray were considered, however, sleeving has inherent limitations on a bore with keyways and flame spray was considered too hazardous.
Selective brush plating was used as a cost and time efficient alternative, surpassing expectations throughout the process.
Many in the power generation industry prefer on-site brush plating as a way of avoiding rack marks from tank plating. These inevitably require additional ‘touch up’ work after the tank process - a time intensive and inefficient two-pronged method of repair, which can be avoided with the use of selective plating.
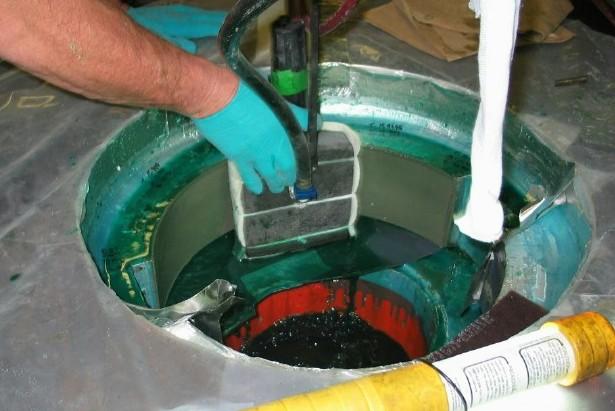
Are you ready to learn more?
On January 29, 2020 SIFCO ASC will be delivering a webinar, Conducting Business: Maximizing Profits by Reducing Turbine Downtime. Created specifically for project managers, process or repair engineers, plus generator specialists and those involved in the maintenance, treatment and resurfacing of critical components for the power generation sector. This webinar will support you in:
- Understanding the basics of the selective plating process
- Learning about which industry and commercial specifications the SIFCO Process® meets
- Exploring real examples of critical component repairs and enhancements
- Understanding the benefits of selective plating over alternative surface finishing processes
To register your place, click here. Or for more information on selective plating, visit www.sifcoasc.com.
About SIFCO ASC
SIFCO ASC applied Surface Concepts provide practical, cost-effective selective brush plating solutions to improve part performance and reduce manufacturing costs through corrosion protection, increased wear resistance, increased hardness, improved conductivity, anti-galling or slip. SIFCO ASC surface enhancement technologies and brush plating services have been utilised for over 50 years on both OEM components and on parts requiring refurbishment in the aerospace, oil and gas, general industry and power generation sectors.