ANCHOR BOLTS FOR ROTATING MACHINERY
/ ALPHATEC ENGINEERING – GROUTING SPECIALISTS /
This article expands on the way anchor bolts are usually installed, the associated problems, and suggests a much better way of doing things.
THE STANDARD METHOD
There are 2 standard methods of installing anchor bolts in a concrete foundation: direct embedment in concrete, or grouting into a reservation made into the concrete block.
The former method relies on precise templates being designed and installed, either inside the foundation, or outside it, supported on, or above the formwork. It is tricky and expensive, and is therefore little used these days.
The second method is slightly better, as the need for more steelwork inside or around the foundation is avoided, but brings with it a number of intractable problems. Ideally, the anchor bolts (foundation bolts, if you prefer) should go right through the main foundation, in order to maintain the concrete in compression, but this means the bolt holes would be 2 or 3 metres long in many cases, and the mechanics of designing and executing a reservation of this depth will defeat most contractors.
So the bolt holes are typically 1 to 1.5 m deep, which is already challenging if the cross-section of the hole is 150 to 200 mm square, a very common size. Some design engineers get creative and design holes that are tapered, being wider at the base than at the top. Assuming wooden forms are used, removal of these becomes extremely complicated. Expanded polystyrene (PS) is often seen as the magic material to use for “blockouts”, as it is light and easy to handle, and can be dissolved with a little acetone once the concrete is set.
However, some PS will always remain attached to the concrete wall, unless it is mechanically cleaned by high-pressure water, sand-blasting (both extremely rare), or manual scraping, which is often done, but mostly ineffective.
Alphatec Anchor bolt system
THE PROBLEMS THAT ARISE
On occasion, the designers will make large reservations to facilitate forming and their removal, but this then requires an enormous volume of grout, which when epoxy grout is specified, means a huge mis-application of resources.
A large hole in the foundation, open for an extended period of time, means water, dust, dirt, and oil will collect in it, and must be emptied out. “Many times, cleaning those holes is obviated/forgotten; because not always is possible to ensure the access since once the equipment is in position turns difficult to give a good cleaning, if precautions have not been taken before.”
If cement grout, or plain concrete is used to grout the bolt, the question to ask is: how much bond between the grouting concrete and the foundation can we expect to achieve? Answer; very little.
How much bond strength will exist between the bolt and the grout? Answer: very little.
What happens when the bolts are tightened to the proper tension (more on that particular subject later)? The bolt stretches, and the cross-section reduces, opening a tiny separation between bolt and grout. This applies to all bolts grouted into the foundation with anything other than EPOXY GROUT.
Once there is the faintest separation between bolt and grout, oil will find its way in.
Operation of the machine will cause vibrations - however small, which will cause the oil to penetrate further and further, until the bolt no longer has any true connection with the foundation.
SO WHAT IS THE SOLUTION?
Now we need an injection repair, and this has proved to be effective in many projects. We drill a hole towards the base of the anchor bolt, install our injection and vent tubes attached to a rebar, inject the ALPHATEC® 342 resins under high pressure which forces the accumulated oil to the surface. As soon as the resin flows clear, injection is stopped, and the resin allowed to cure overnight. The bolt can normally be tensioned to the specified torque the following day.
Still, the best way to avoid anchoring problems is to use our “Stress-Free Anchoring system”. The diamond core drilled hole is sized for the anchor bolt to be placed, approximately 3xD. The fully-threaded rod is isolated, and the anchor hung from the machine flange, or soleplate.
After initial alignment, the bolts can be grouted up to the chipped surface of the concrete. Once the grout is cured, the bolts can be used to hold the machine down in areas where needed, while the jacking screws, or ALPHAPADs®, hold it up, allowing for a very precise alignment.
Finally the bolt should be tightened to 70% of its yield strength, or to 450 N/mm2 stress for grade 8.8 material. We advocate the use of Superbolt® tensioners to be sure of getting the correct tension in the bolts, and can supply and install them as part of our service.
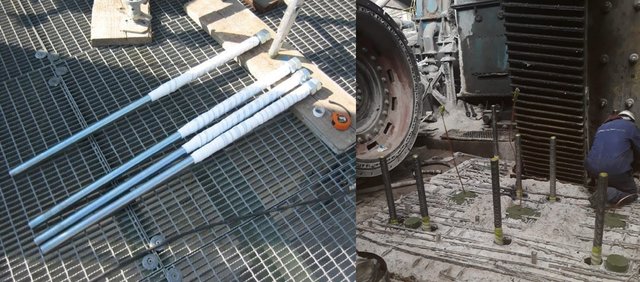
Alphatec GreenEpoxyGrout
Alphatec Engineering S.L.
Global services with more than 4000 contracts in 57 countries
T +34-961-451-599
E info@alphatec-engineering.com
W alphatec-engineering.com