Mobile Energy Solutions
Manufacturing
Development
Commodities
Consulting
Certification
Battery pack production for industrial applications
For many years the OMNITRON name has been synonymous with quality, flexibility and reliability. Concept development accompanied by tailor-made advice, specific proposals and detailed project documentation are just some of the services offered by this well established company.
At the company’s own battery pack production facility, our highly qualified experts bring together know-how acquired over decades with the innovative ideas of a dynamic service provider.
In this sector, OMNITRON GRIESE GMBH develops comprehensive solutions to suit customer-specific parameters. Several sophisticated production lines are available for project-based assembly.
Special ESD (ESD = Electro Static Discharge) workplaces and work areas eliminate problems arising from electrostatic charges, completely preventing damage or subsequent damage to electronic products at OMNITRON.
Visitors are always welcome at the OMNITRON production plant, which is certified in accordance with DIN EN ISO 9001 and 13485. Staff will be pleased to provide information about the ongoing assembly process and quality checks conducted there.
1.
Development and Design
2.
Initial Samples and Approvals
3.
Production Planning
4.
Series Production
5.
Final Inspection
6.
Packaging and Shipping
Click on the battery bars
1. Development and Design
Our engineers and technicians work with you to develop solutions designed to fit your task. Benefit from the experience of our highly-trained employees, particularly regarding both the safety of your product and the latest legal requirements for lithium ion technology. We offer you comprehensive advice and the optimum battery solution for your application.
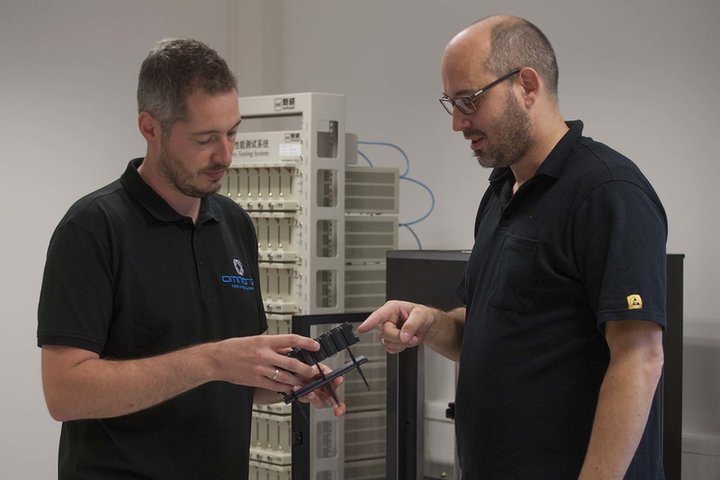
2. Initial Samples and Approvals
We create an initial sample on the basis of your specifications and requirements, and test this for full function and capacity. Via our in-house rapid prototyping process, we subsequently produce a scaled 3D model of your case upon request. We send you the samples together with our test report. After this, we only proceed with your personal seal of approval. We provide you with support as you seek legal approvals such as UN certification and, optionally, UL and IEC certifications, as well as the accelerated CB Scheme certification.
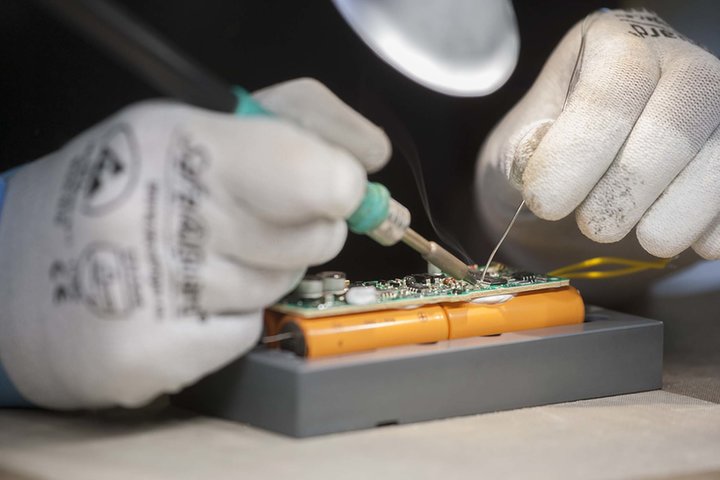
3. Production Planning
Before we embark on series production on your behalf, we devise the optimum workflow and produce individual auxiliary tools as necessary. During the pilot series’ planning phase, our sales, project development and production specialists are at your side to provide additional advice. Series production starts once we have received your final approval.
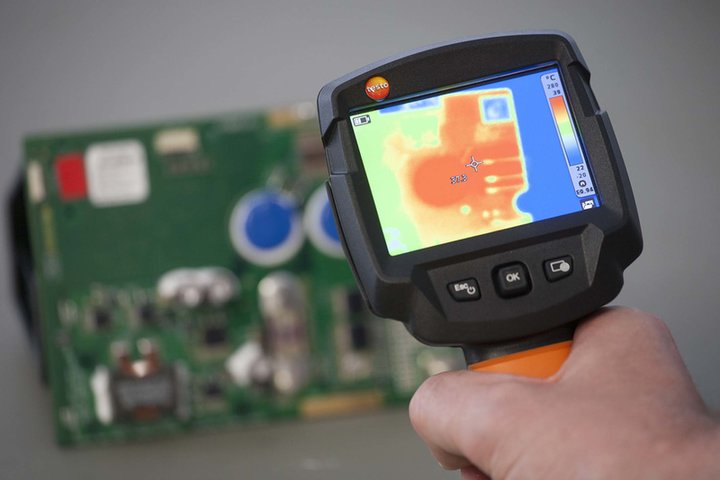
4. Series Production
During series production – under ESD conditions – continuous quality control ensures that the desired final result is achieved. Measurement checks against drawing, heating cabinet testing, voltage and capacity tests, functional testing of individual components, tensile tests on cables and plug-in connections – our spot tests, especially those conducted in the start-up phase, are ultramodern and comprehensive.

5. Final Inspection
Final inspection ensures 100% functional safety. Individual tests during production are fully documented, in accordance with our DIN EN ISO 9001 or 13485 certification. Our test certificate includes all test characteristics and provides data on tests conducted and their outcomes. The works certificate documents the quality of the individual components used.
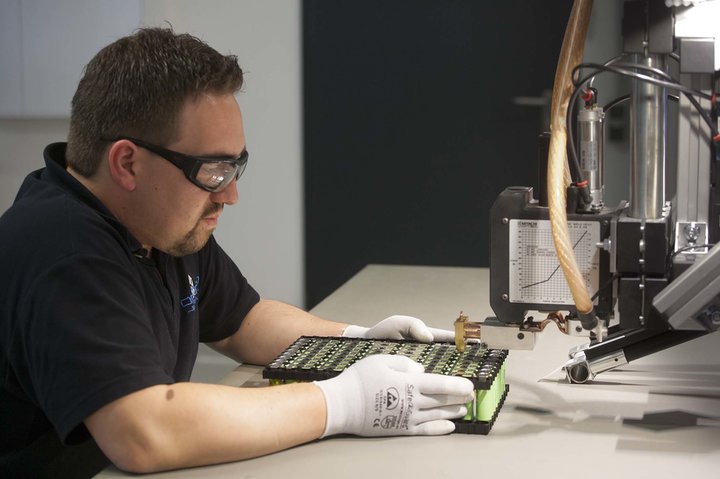
6. Packaging and Shipping
Packaging and shipping are performed in compliance with your individual specifications, such as batch identification to facilitate traceability. Our employees are trained in the handling and transportation of dangerous goods. All current legal requirements are invariably observed. After all, we would like you to receive our high-end product safely and in perfect condition.
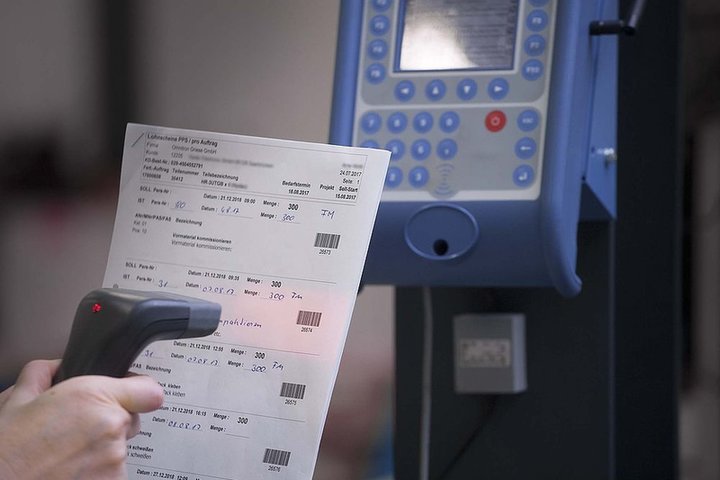