Company Insight
Sponsored by Watlow
Electric process heaters: a key source in decarbonization
The use of heat is crucial to the processing and refining of hydrocarbons. Historically, fossil fuel-based heaters have been the go-to solution for these applications. However, driven by the increasing urgency to reduce carbon dioxide emissions and achieve decarbonization objectives, engineers are investigating the viability of using electric process heaters in these operations.
Main image credit:
Here, Dennis Long, director of engineering at industrial technology manufacturer, Watlow, explores how process heaters can facilitate decarbonization efforts.
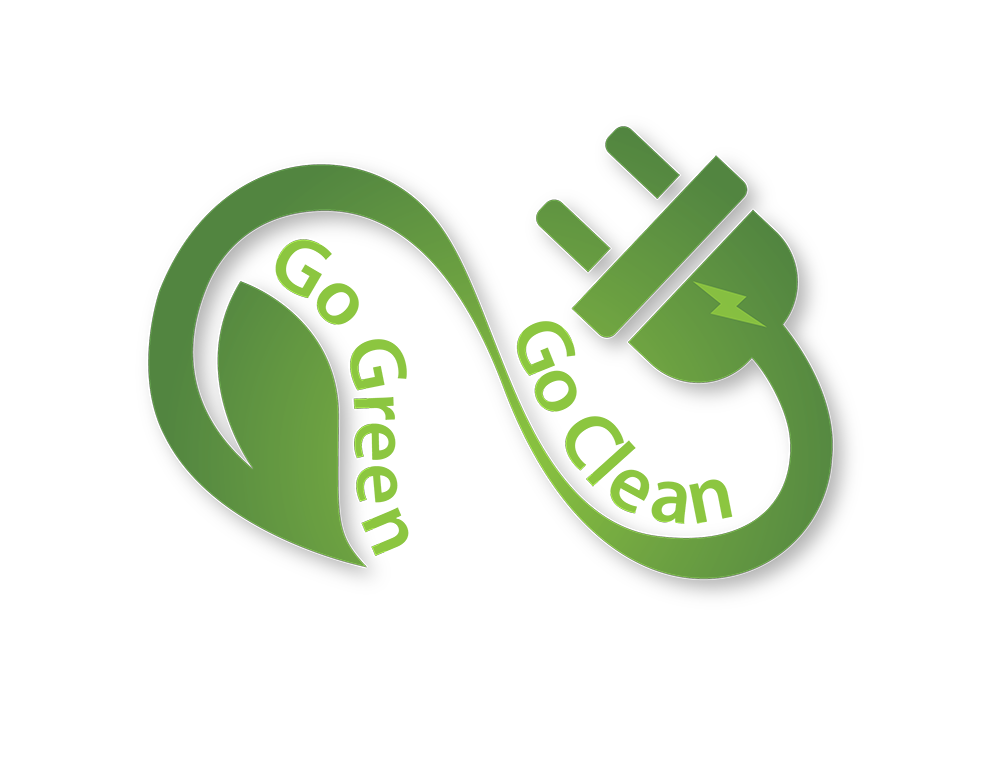
Process heating is a significant source of greenhouse gas emissions in the industrial sector, and so replacing fossil-fuel based heaters with electric ones running on green energy should yield significant progress towards decarbonization goals.
Specifically, replacing fossil fuel heaters with electric heaters would allow for a reduction in Scope one carbon dioxide emissions. Scope one emissions, defined by Buehler, are the direct result of burning fuels like natural gas or fuel oil for process heating. Scope two emissions result from the need to import energy, while Scope three emissions are produced while using a product such as the emissions from vehicles on the road. All three types must be reduced to hit global decarbonization targets.
Current limitations
A survey conducted by Watlow for its customers and prospects has revealed that 90 per cent of oil and gas leaders are already actively engaged in decarbonization efforts. Hydrocarbon processors are no longer focused on if they should decarbonize, but how.
So why aren’t electric process heaters more ubiquitous in the energy sector today? Surprisingly, familiarity might be the main reason. Until now, such heaters have played only very narrow roles in hydrocarbon processing and were usually smaller, operating at lower voltages. Although larger heaters are easily imaginable, engineers recognize that a number of questions arise when it comes to their control and maintenance. Ultimately, no one wants to be first into the water when it comes to running larger medium-voltage thermal systems.
The good news is that modern electric heaters can provide the same, if not improved, performance that hydrocarbon engineers have come to expect from fossil fuel powered heaters.
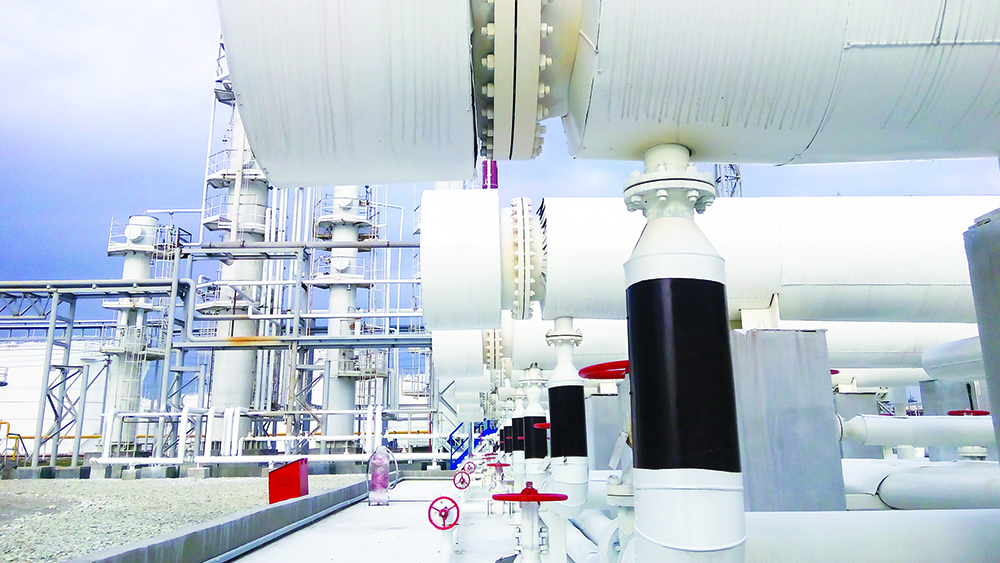
Hydrocarbon Processing.
Maintaining consistent control
Some of the most common questions about larger process heaters have to do with control. What additional elements are needed to ramp up the heater? How is temperature monitored and controlled? What additional safety precautions are needed?
The lack of traditional usage of larger electric heaters for heating processes in the petrochemical industry does not imply that the technology is unproven. On the other hand, proven power switching devices have been employed for low voltage electric process heaters and medium voltage motors across various industries for an extended period, establishing a well-tested capability to regulate voltage.
Programmable logic controllers (PLCs) and similar power management systems bring heaters online in ways that prevent problems for other devices connected to the same power source. The heater and controller are part of one closed-loop system, which streamlines integration and yields more control over the entire system.
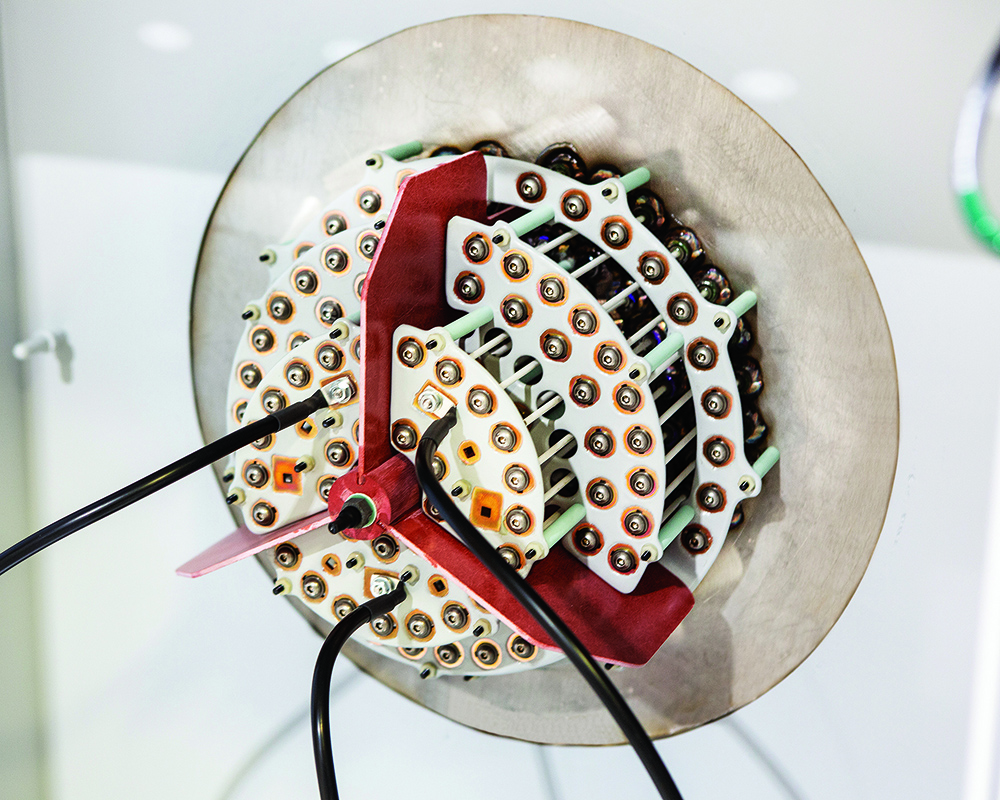
Medium Voltage.
Thermal expertise
Thermal solution leaders like Watlow are solving the most challenging and essential thermal problems surrounding decarbonization. For more than a century, Watlow has been working to break down the barriers to energy transition to provide clean, efficient and reliable ways to electrify processes traditionally heated with fossil fuels.
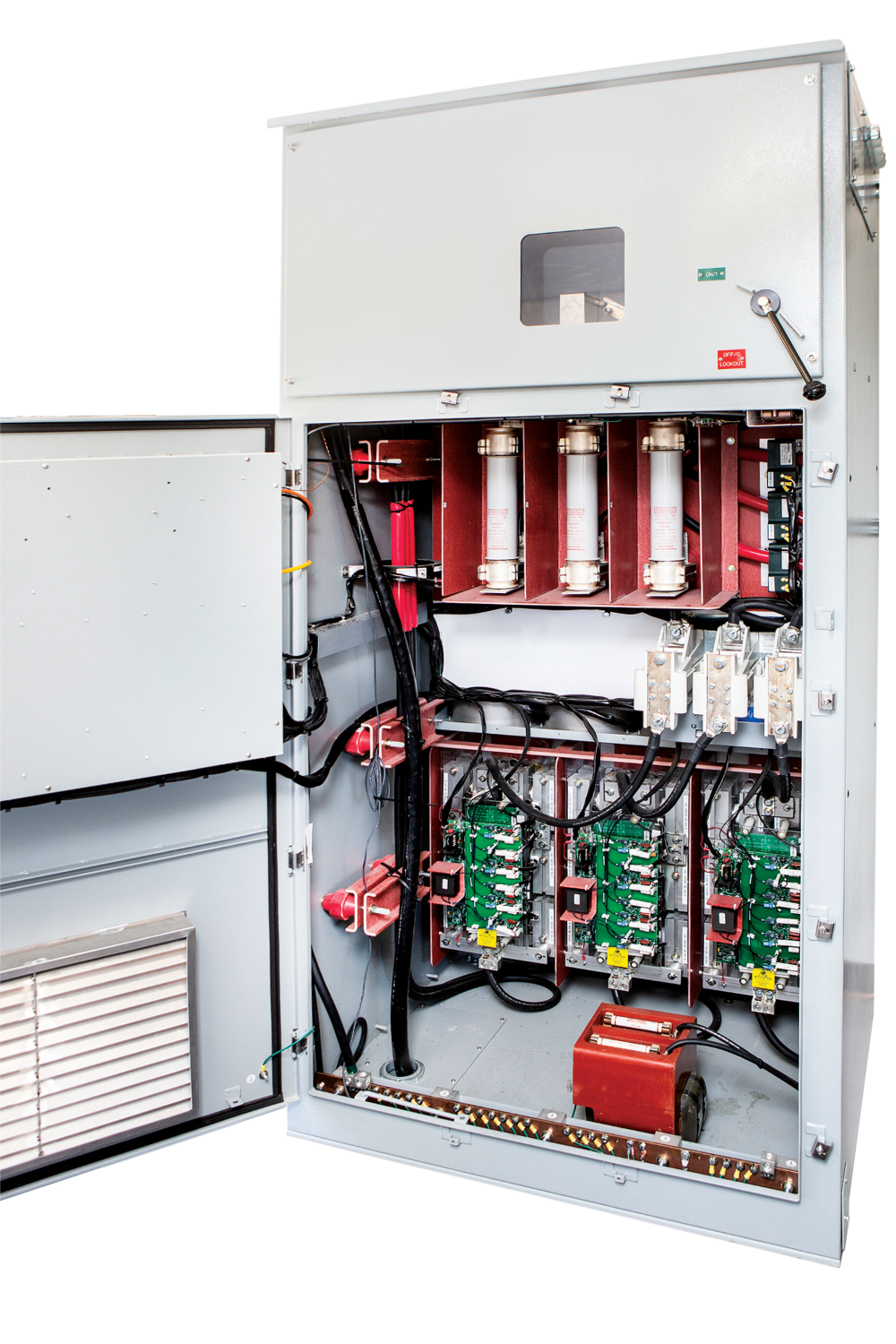
POWERSAFE panel.
Its POWERSAFE solution — a medium voltage heating solution that combines an electric heat exchanger, process controller and power system — is a safe, reliable and clean replacement for fossil fuel alternatives in process equipment.
The system also comprises as an isolated low voltage enclosure, including a human machine interface (HMI) and PLC. It’s been proven to operate safely and reliably at up to 7200V POWERSAFE also offers a flexible combination of a silicon-controlled rectifier and contactor circuits up to 25 megawatts within a single control package, delivering high-efficiency power to reduce the size and weight of the solution, while providing a clean, safe asset for engineers tasked with decarbonizing thermal systems.
It also incorporates a flexible combination of a silicon-controlled rectifier (SCR) and contactor circuits up to 20 MW, delivering high-efficiency power greater than 99 per cent, which reduces the overall size and weight of the solution.
Understanding electric process heating systems now can alleviate future energy transition challenges. Engineers have come to recognize two key factors. Firstly, there are significantly more opportunities for using electric process heating systems with fewer size limitations than previously believed by energy and environmental engineers. Secondly, field applications have demonstrated effective control of these large-scale heating systems, showcasing precise management of process and surface temperatures. Collaborating with a dependable partner to electrify process heating systems stands as a reliable approach to advancing climate action goals while sustaining productivity and profitability.
About Watlow:
Founded in 1922, Watlow strives to be the leading provider of thermal solutions for the world’s most demanding applications. Utilizing our advanced technology, leading companies apply our thermal systems which are ideally suited for vital applications such as clean and environmentally-friendly energy systems and processes, front-end semiconductor processing and lifesaving medical and clinical equipment. Since 1922, Watlow has grown in product capability, market experience and global reach. The company holds more than 1,100 patents and employs 6,000 team members working in 12 manufacturing facilities and five advanced technology and development centers in the United States, Mexico, Europe and Asia. Watlow covers 95 countries through sales and distribution offices around the world. The company continues to grow, while the commitment remains the same – to provide its customers with superior products and services for their individual needs.
If you want to ensure you keep up to date with the latest content from Watlow, visit the website: www.watlow.com/news
Contact information
European headquarters: Johann Lainer
Watlow Plasmatech GmbH, Brennhoflehen-Kellau 156, 5431 Kuchl, Austria
Tel: +43 6244 201 29-0
E-mail: jlainer@watlow.com
Website: www.watlow.com