
How to prevent premature failure of a coating?
The best definition of a protective coating system is: ”Transparent or colored product that forms a film and protects the surface on which it is applied against influences from the environment”. This means a barrier is created between the steel and environment in order to prevent corrosion. This barrier is applied as a liquid material that adheres to the steel substrate and forms an oxygen, chemicals (“salts’) and water(moisture) proof film. In most cases, this film is less than 1 mm thick and more than 300 μm. It is often required that this thin film protects the steel for more than 20 years, preferably maintenance free.
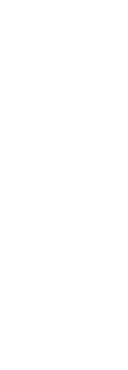
Type of failures
The main failure of a coating system when properly applied is losing its main barrier function. This means the coating cracks. When the cracks grow through the coating oxygen, water and chemicals (“salts”) can reach the steel substrate, resulting in corrosion.
We determine three stages of cracking:
● Micro-cracking
(superficial cracks up to the upper 100 μm)
● Meso-cracking
(cracks reaching up to the top of the primer layer)
● Macro-cracking
(cracks reaching up to the steel substrate)
When a coating system is taken into use it will degrade under the exposition circumstances, such as UV-(sun)light, thermal shocks, water etc. In due time the coating will start to crack and finally fail. There are different types of methods to control this, such as EIS (electrochemical Impedance Spectroscopy) but a very reliable one is microscopical analysis of cross sections.
It is clear that serious problems occur when the coating system shows cracks shortly after application. This is especially the case with coating materials that show a high degree of internal shrinkage after application. These coatings exhibit significantly lower tolerance to application conditions and can easily crack and delaminate at edges, welds and locations where the film thickness is higher than allowed.
Surface preparation
“If you fail to prepare, you prepare to fail*)” is a well-known statement in the protective coating business.
Based on this some claim that more than 70-80% of all premature coating failures is due to bad or insufficient surface preparation. According to our experience and damage analyses in Germany Lit.1), it can be concluded that inadequate processing and / or incorrect application has caused between 43% and 68% of the premature coating failures, such as:
● The steel surface was too heavily contaminated with soluble salts (ISO 8502-6/9);
● and/or did not fully comply with the requirements of blast-cleaning to Sa standard (ISO 8502-1)
● and/or the preparation grade of welds, edges and other areas with surface imperfections did not comply with the requirements the standard (ISO 8301)
Tolerant coating products
A general description of a coating system is therefore no guarantee for performance. Only real-life experience and/or intelligent testing will reduce risks in more reliable way.
The main weaknesses of coating systems are very material (recipe) related and will only be revealed by real outdoor exposure and/or relevant tests. The main weaknesses of less reliable products are:
● Insufficient tolerance towards less optimal surface preparation such as remnants of salts, insufficient rounding of edges, resulting in debonding.
● Buildup of too high internal stresses resulting in cracks near welds, edges, bots etc. And resulting in peeling of near damaged locations.
Risks
At present it can be noted that products are primarily designed to pass tests. All prescribed tests are performed on small and flat panels without any relation to practice. Detachment of the coating can usually be observed at the edges, welds, bolts, etc. and rarely on flat surfaces. When a Norsok approval becomes more important than relevant track records, we find that it is time for change.
The coating application process must be controlled according to current specifications in terms of, among other things, dew point, dry film thickness, adhesion, etc.
However, problems with a major impact on the quality and performance of the coating, such as internal (shrinkage) stresses, curing, solvent, retention, etc. are not checked because they are not included in the standards. Moreover, in most cases there is insufficient awareness about the impact of these uncontrolled parameters. There is a complete dependence on general protocols that actually give the illusion that the most important risks have been sufficiently reduced.
Bjond approach
The realisation of a paint job resulting in a maintenance-free coating system, for more than 20 years, requires not only require focus of the application process. This is often translated in extensive (useless) QC during the substrate preparation and coating process.
We are convinced that this can only be achieved by a balanced approach on three main issues:
● Process
● Product
● People
Selecting the right materials, writing the best fitting specification related to the process and people is the basis for achieving a high-end paint job and the work for real experts. Only on such a solid basis can Nace and/or Frosio inspectors offer meaningful monitoring and inspections.
Bjond Innovation offers in this area high-end fit for purpose support based on broad field experience, knowledge of coating materials and an extensive network.
Consulting, inspecting, innovating and offering knowledge-intensive services are the activities of Bjond Innovation. This company, based in Belgium, is engaged in the protection of steel and concrete in the broadest sense of the word. "You can say that we are experts in coatings, building materials and selecting materials," says owner Jo van Montfort. "But our specialism lies mainly in the field of corrosion protection, and customers hire us for this. Inslated in extensive (useless) QC during the substrate preparation and coating process.
References
We can offer many references (>15-20 years) for which this approach has been successfully applied, such as a project in The Netherlands, steel constructions of the Eastern Schelde Storm Barrier (Oosterscheldekering, 33 steel doors Roompot).
Based on market search and testing, finally a coating system was selected for this project. This system was applied as a repair on a surface that was heavily attacked by pitting corrosion, and then intensely prepared by drilling out the pits followed by water cleaning and grit blasting. Because the substrate was very uneven, a coating material was required with relatively low internal stresses and high tolerance for substrate imperfections. Weak point of this system was that it was a multilayer system that contained solvents, making the application more critical to failures.
cost
The construction, installation and maintenance of offshore wind turbines and their foundations is, because of the difficult accessibility, extremely expensive. The typical coating repair costs offshore are a factor of 100-3000 times higher than comparable onshore repairs.
For the offshore wind industry, special attention has been paid to cost reductions of the turbine itself. However, it must be realized that, according to Weinell e.a.lit.1), only about ¼ of the lifetime cost of the service is usually allocated to the wind turbine itself. Costs related to other elements such as maintenance of the substructures (monopile and transition piece) of offshore farms represent more than half of the service life costs.
This means that there is a great demand for improvement of the corrosion protection of substructures with coatings.
In our opinion it is possible to improve by attracting experts where necessary instead of increasing the useless QC. We are convinced that for steel structures in general and specifically offshore wind foundations, the costs can be significantly reduced, and the maintenance-free lifespan can be extended to 25 years, as soon as the industry dares to look beyond the existing standards and protocols.