Engie uses IoT to monitor operational performance and fast-track decarbonisation
Engie’s CRIGEN Lab is investing in digital twinning and IoT technologies to optimise the operation of its hydrogen prototypes. The company has created a digital twin, using PTC’s IoT platform, to enable the running of 3D simulations of its hydrogen industrial furnace.
The digital twin is connected to an industrial IoT platform, which allows the physical separation of the industrial equipment from the digital twin. IoT technologies are used to collect and centralise data from multiple types of sources and the company uses a hybrid cloud to enable greater control over the system and greater flexibility in data recovery. This project aims to optimise the operation of the conversion to hydrogen and speed up the company’s energy transition.
The digital twin system enables the real-time optimisation of energy and environmental performance of equipment. It also provides a greater opportunity for predictive monitoring and maintenance of the aging of physical equipment, thus reducing maintenance costs long term.
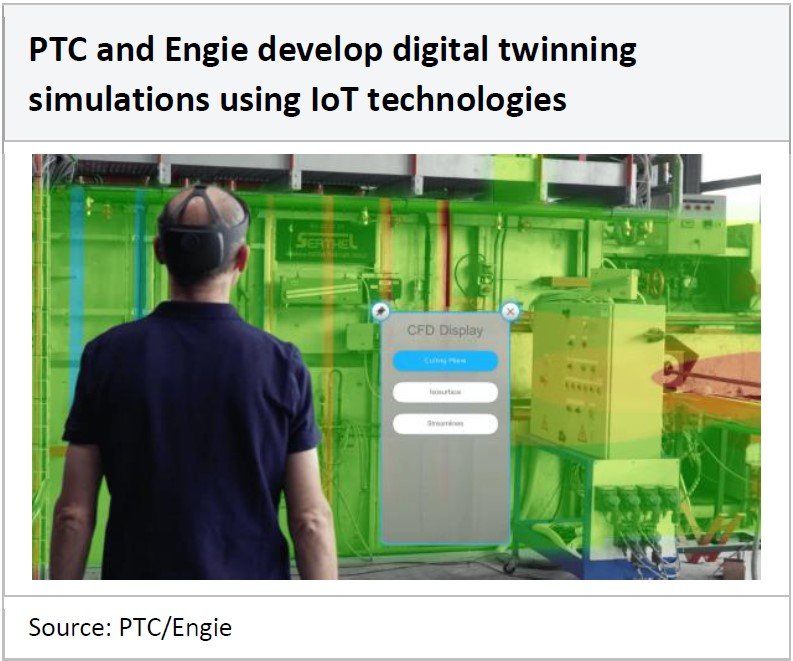
Equinor introduces remote monitoring for offshore operations
Norwegian oil major Equinor is regularly experimenting with new technologies for enabling performance optimisation at its offshore assets. In one such study in August 2017, it decided to evaluate the potential of digital twins in facilitating remote monitoring and operations of unmanned production platforms, using IoT technology for live data collection.
It also intended to understand if this technology could deliver superior agility during the field development process. The company wanted to cover a wide range of topside activities in this study, including hydrocarbon production, platform maintenance, as well as supply chain and logistics management. The scope was purposely kept broad to assess the overall benefits that could be derived by deploying digital twins in oil and gas operations.
Kongsberg, whose digital twin system was used in this study, developed custom user-friendly apps for interfacing with the twin. This system could handle data related to project design, construction, operation, maintenance, and supplementary functions, such as logistics and finance. It could also run simulation tests and allow users to visualise the outcome.
For six months, Equinor ran several tests with this digital twin and was impressed with the results. Besides achieving estimated savings in capital and operating expenses of 30 and 50% respectively, the twin could also boost profits by 10% over the operational life of the production platform.
Moreover, the system could drive productivity by improving collaborations. It also had the potential to reduce net emissions by optimising resource utilisation and predicting equipment failures.
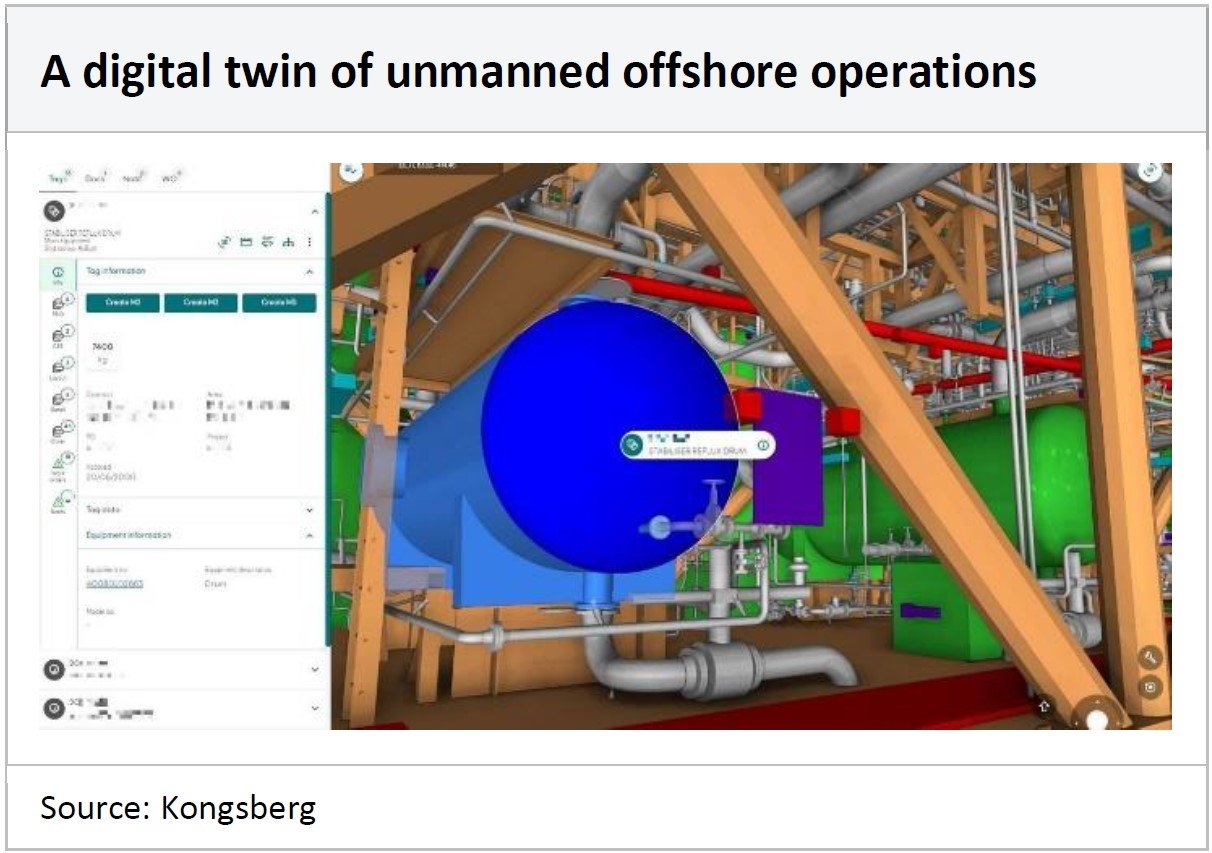
EDF’s use of IoT for predictive maintenance of equipment
EDF Energy has been extensively expanding its use of IoT and AI technologies for predictive maintenance. The company intends to collect data from sensors installed in major asset components to improve production and anticipate aging.
So far EDF has entered into a framework agreement with OROS to carry out advanced assessments of rotating equipment, used for hydroelectric and nuclear production, as part of its predictive maintenance procedures. It utilises OROS devices to precisely determine the warnings to be triggered by the permanent vibration monitoring systems and plan the corrective actions that will potentially be required to ensure the continuous production of electricity.
Also, the EDF Renewable Energy division partnered with ONYX to deliver vibration analytics to improve EDF Renewable Services Operation & Maintenance (O&M). ONYX serviced over 7,400 turbines, more than 40 equipment types, and 720 inverters that generated about 9.3GW of electricity.
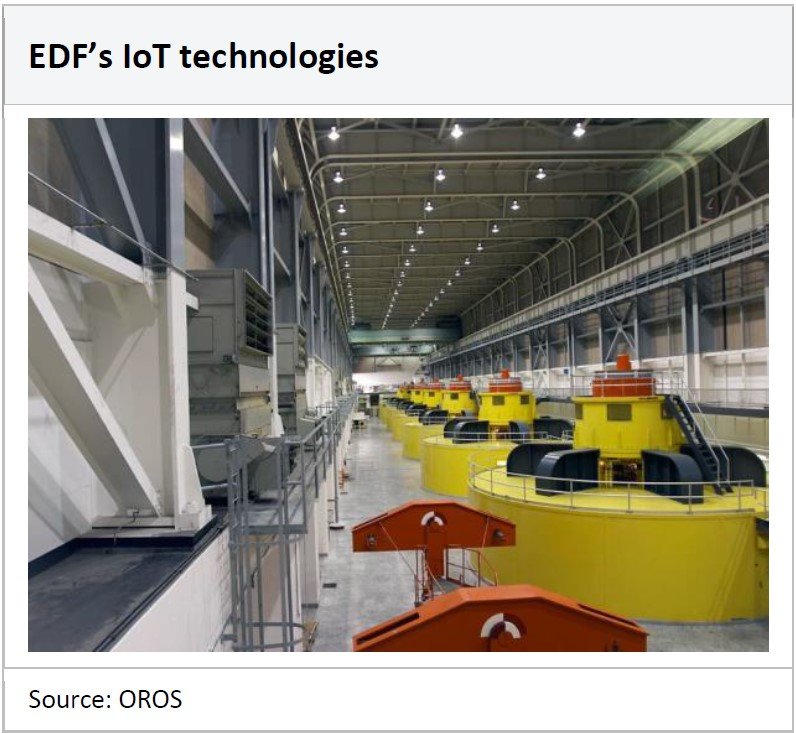
SSE Airtricity is developing an IoT-connected operating system
SSE Airtricity is an official project partner of the European-funded IoT2Cloud Operating System (ICOS) project, which uses IoT and AI technologies to help consumers reduce energy waste and costs. The ICOS project is developing an operating system to connect different computer processing and storage capabilities, using IoT, edge, and cloud platforms, so that the data can be managed for energy decisions.
SSE Airtricity is designing the energy management and decision support system that uses data collected from ‘smart homes’ and using AI, the system will monitor the user’s energy consumption and make decisions over whether energy should be produced, used, or stored. The smart homes are equipped with IoT-connected smart meter devices and various energy transition technologies, such as solar panels, electric vehicles, and heat pumps.
The desired outcome is for the AI model to reduce the consumer’s energy demand by scheduling the use of energy away from peak times and increasing the use of renewable energy sources.
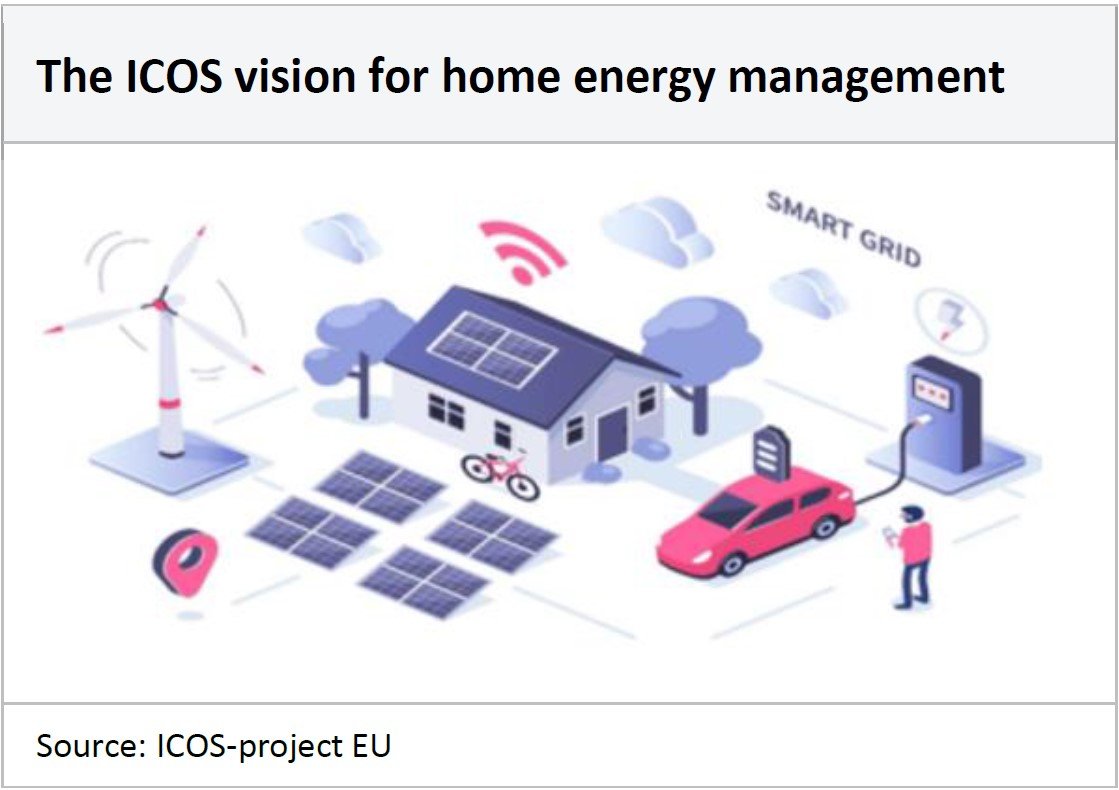
The world’s largest wind farm has been digitally transformed with IoT technology
Ørsted is a global leader in offshore wind power and supplies large-scale and cost-competitive offshore wind energy, onshore wind energy, and solar energy solutions. It relies on a digital strategy to enhance productivity and reduce costs.
The company has invested in digitally connecting its Scottish offshore wind farm through a partnership with Vodafone, which now provides 4G data service. They have then combined this by partnering with Microsoft to use cloud technology to store the data collected from the farm and Microsoft’s advanced analytics and artificial intelligence services to provide live analytics of the data collected. The company aims to save time and resources through this investment, preventing unplanned shutdowns or power outages from the wind farms.
The plant, situated in the North Sea off the coast of Scotland, is the world’s largest wind farm and provides power to millions of people living in the UK. Data analytics, automation, and predictive maintenance are all playing a significant role in helping wind turbine operators manage the costs of unplanned repairs.
Ørsted’s investments in IoT and related digital transformation technologies are helping to optimise the utility gained from the data collected from its 1,300 offshore wind turbines and provide insights for predictive maintenance. This will save the company time and resource costs for turbine repair and maintenance in the longer term.
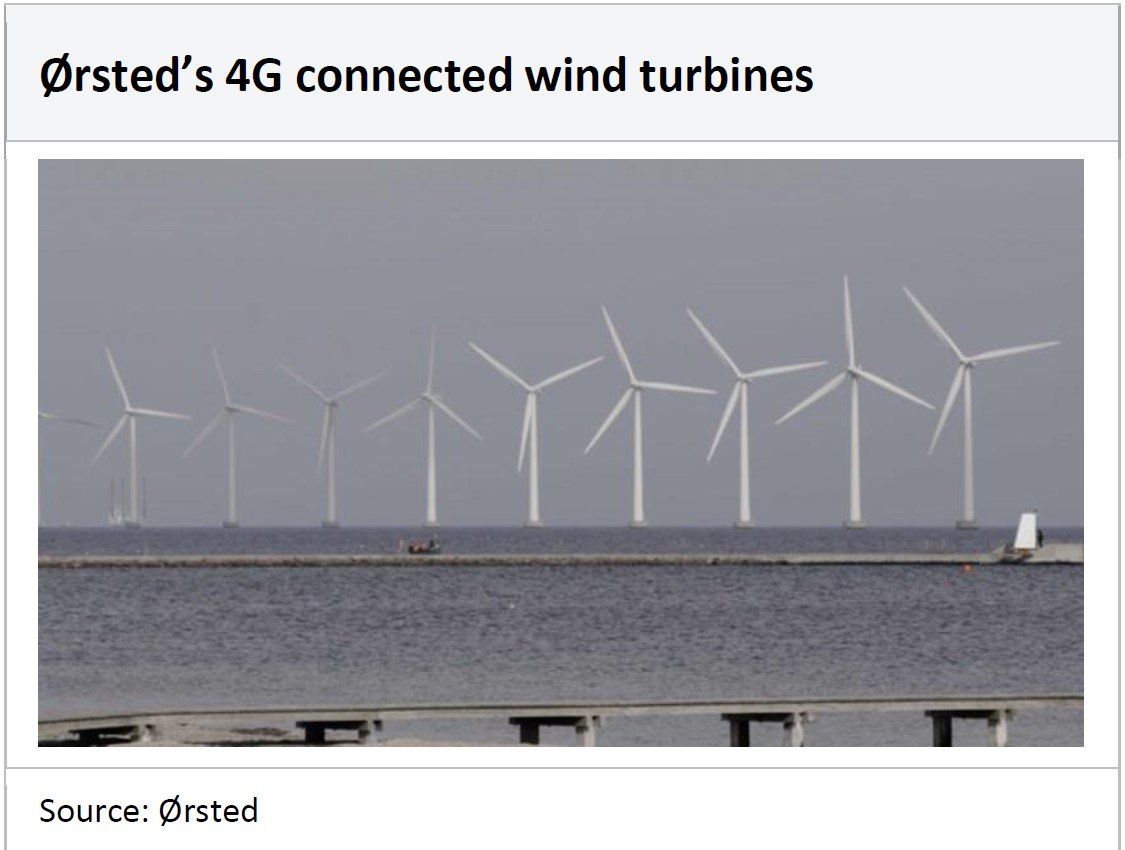
GlobalData, the leading provider of industry intelligence, provided the underlying data, research, and analysis used to produce this article.
GlobalData’s Thematic Intelligence uses proprietary data, research, and analysis to provide a forward-looking perspective on the key themes that will shape the future of the world’s largest industries and the organisations within them.